The field of additive manufacturing, colloquially known as 3D printing, at Trier University’s Environmental Campus Birkenfeld continues to grow.
The Institute for Operations and Technology Management is the lead partner in the INTERREG project ComPrintMetal3D “Application-related comparison of different 3D metal printing processes” with the project partners htw saar, Université du Luxembourg and Any-Shape (Belgium) S.A. Furthermore, several strategic partners, especially small and medium-sized enterprises (SMEs), are involved in the project.
The project aims to provide SMEs in the Greater Region with a guide to additive manufacturing of metal components.
There is very strong momentum and an increasing number of process options in this emerging manufacturing sector. This and a lack of overview makes it difficult for SMEs, despite great interest in additive manufacturing, to efficiently choose the most economical manufacturing option. To make this possible, a step-by-step guide is being created that examines and presents filament- and powder-based printing methods. That is, on the one hand, the selective laser melting (SLM) process uses a laser to melt fine metal particles and produce a metal component layer by layer. Filament-based production of metal components is carried out, among other things, on desktop printers familiar to home users. Here, the filament is melted from a metal/plastic mixture layer by layer using the FFF (fused filament fabrication) process and printed. The plastic is then removed in a rebinding process before the component is sintered into the finished object.
In the project, samples are produced and investigated using the different manufacturing methods in order to be able to determine basic material properties and compare them with each other. This creates a basis for the production of demonstration objects from the business areas of the consortium partners.
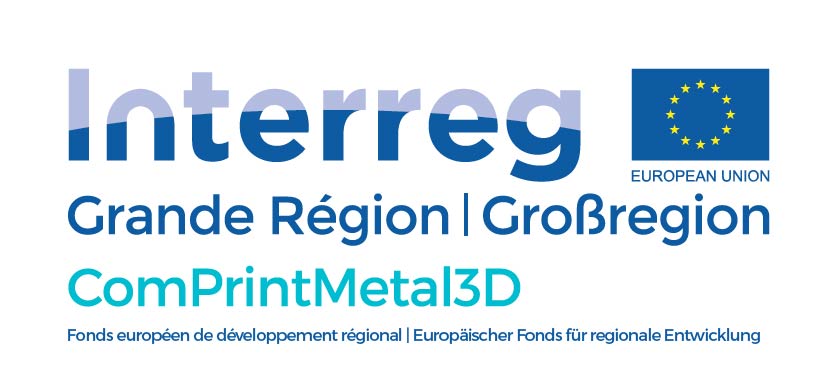